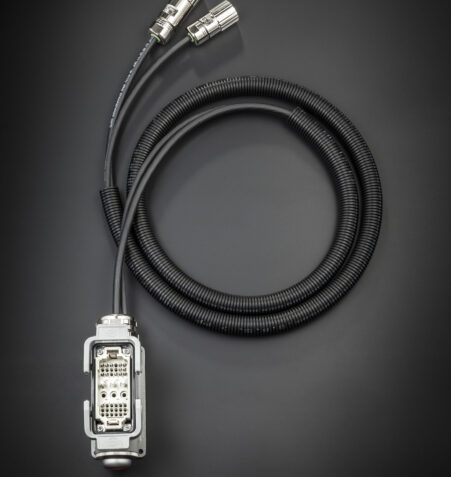
Robotics
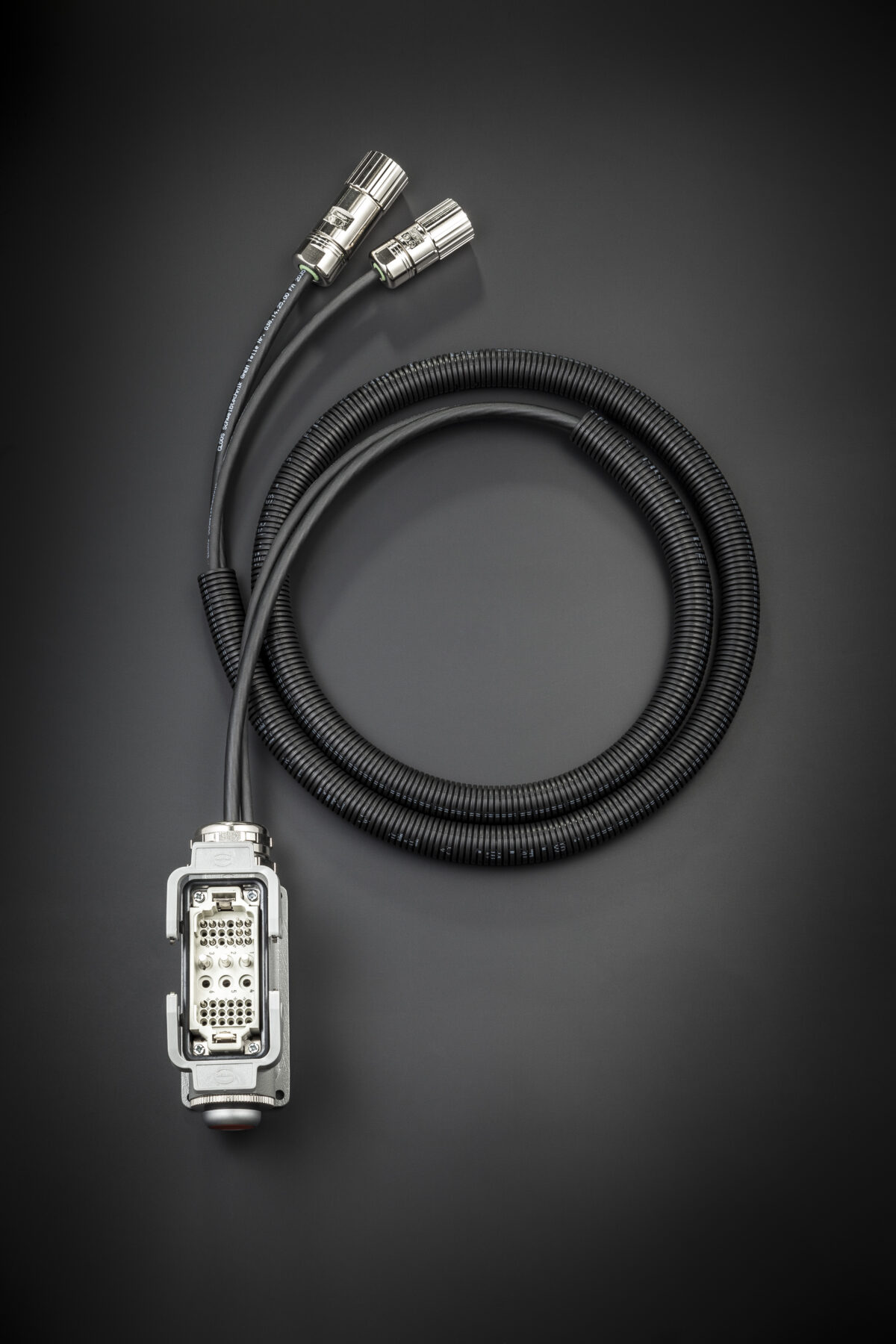
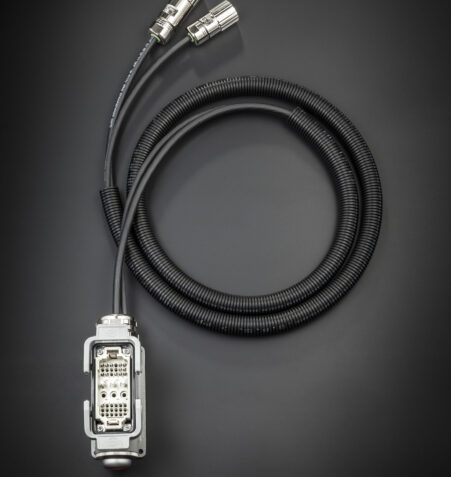
LED Industrieleuchten im Maschinenraum oder am Montageplatz gefertigt in Deutschland – robust, langlebig und effizient. Perfekt für jede Anforderung. Dafür sorgen wir.
LED Maschinenleuchten müssen exakt die Anforderungen erfüllen – von der Abdeckung bis zur Schutzklasse. Ob als Aufbauleuchte oder Einbauleuchte.
Entdecken Sie unsere vielfältigen LED Aufbauleuchten für Maschinen & Anlagen – kompakt, flexibel & robust! Lassen Sie sich jetzt beraten!
Entdecken Sie LED Maschinenleuchten als Einbauvariante – optimale Ausleuchtung ihrer Maschine, hohe Schutzart und extrem robust – ideal für den Einsatz von Kühl- und Schmierstoffen. Jetzt informieren!
Setzen Sie auf individuelle LED Sonderlösungen, die perfekt zu Ihren Anforderungen passen – profitieren Sie von Expertise & Kosteneffizienz.
Entdecken Sie innovative LED Signalleuchten: Beleuchten & Signalisieren gleichzeitig! Optimieren Sie Industrie- & Maschinenarbeitsplätze. Jetzt informieren!
Die Eigenschaften unserer LR40 Standard ergänzt um die Signalfunktion einer RGB Leuchte.
Unsere Aufbauleuchte LR40-RGBW zum beleuchten und signalisieren ist durch ihre Vielzahl an Eigenschaften ein echter Allrounder. Spannungsversorgung von 24V, robust und optimiert für den Einsatz in besonders rauen Umgebungen, z. B. CNC-Fräsmaschinen mit Spanbeschuss.
Erfahren Sie hier mehr über die Konfigurationsmöglichkeiten der L40-RGBW.
Die Eigenschaften unserer SL Standard ergänzt um die Signalfunktion einer RGB Leuchte.
Unsere Aufbauleuchte SL-RGBW zum beleuchten und signalisieren ist durch ihre Vibrationsfestigkeit, schmale Bauform und einfacher Montage für den Einsatz vieler Industrieanwendungen geeignet.
Erfahren Sie mehr über die Konfigurationsmöglichkeiten der SL-RGBW.
Die Eigenschaften unserer ELN Standard und ELN RGB in einer Leuchte vereint.
Unsere Aufbauleuchte ELN-RGBW überzeugt einerseits durch ihre Bauform bei der lichtstarken rundum Ausleuchtung von Maschinenräumen und verfügt andererseits über eine Signalfunktion durch Wechsel der Lichtfarbe.
Erfahren Sie hier mehr über die Eigenschaften der ELN-RGBW.
Mit unserer ELN-RGB lassen sich z. B. Statusanzeigen farblich visualisieren. Durch das dreidimensionale Lichtbild ist das Signal aus bis zu 180° sichtbar.
Unsere Signalleuchte mit Schutzart IP54 für Arbeitsbereiche mit wenig Platz, drehbarer Halterung, 24V Spannungsversorgung und einfache Montage.
Erfahren Sie hier mehr über die Eigenschaften der ELN-RGB.
Das besondere an unser LED DL ist ihr 2-Kammer- System, welches auf der einen Seite die separate Ausleuchtung des Maschineninnenraums ermöglicht und auf der anderen Seite zeitgleich die äußere Signalisierung visualisiert.
Erfahren Sie mehr über die Eigenschaften der DL.
Kombination aus beleuchten und signalisieren, starke homogene RGB-Beleuchtung über ein großflächiges Lichtbild, Schutzart IP40 – konzipiert für den Einsatz an Montagearbeitsplätzen und industrielle Umgebungen sowohl an als auch in Maschinen.
Erfahren Sie mehr über die Eigenschaften der APL-RGBW.
Erleben Sie ergonomische Beleuchtung mit LED Arbeitsplatzleuchten, die sich Ihren Bedürfnissen anpassen. Memory-Funktion & UGR19 – Jetzt umrüsten!
Wir sind Ihre Ansprechpartner im Bereich der Kabelkonfektionen, LED-Industrieleuchten und Systembaugruppen. Kontaktieren Sie uns gerne. Wir freuen uns auf Sie.
Kompakt, leistungsstark und robust – perfekt für Werkzeugmaschinen und kleine Bauräume. Optimiert für raue Industrieumgebungen. Beständig gegen Öl- sowie Kühl – und Schmierstoffe (Schutzart IP67). In der ESG Variante ist sie zusätzlich gegen Beschuss von Metallspäne und Funkenschlag resistent.
Erfahren Sie mehr über die Eigenschaften der LED KL.
Flache und schmale Bauform, besonders vibrationsfest, 24V Spannungsversorgung und einfache Montage – perfekt für den Einsatz von Arbeitsbereichen mit wenig Platz.
Erfahren Sie hier mehr über die Eigenschaften der LED SL.
Großflächiges Lichtbild, sehr flache Bauform (16,5mm), IP67 geschützt, – Optimiert für raue Industrieumgebungen. Beständig gegen Öl- sowie Kühl – und Schmierstoffe. In der ESG Variante ist sie zusätzlich gegen Beschuss von Metallspäne und Funkenschlag resistent.
Erfahren Sie mehr über die Eigenschaften der LED FLS.
Großflächiges Lichtbild, ultraflache Bauform (3mm), IP67 geschützt, – Optimiert für raue Industrieumgebungen. Beständig gegen Öl- sowie Kühl – und Schmierstoffe. In der ESG Variante ist sie zusätzlich gegen Beschuss von Metallspäne und Funkenschlag resistent.
Erfahren Sie mehr über die Eigenschaften der LED EBLT.
Unsere Anlagenleuchte mit Schutzart IP54 für Arbeitsbereiche mit wenig Platz. Homogene und großflächige Ausleuchtung, drehbarer Halterung, 24V Spannungsversorgung und einfache Montage. Jetzt verschiedene Varianten entdecken!
Die LED Aufbauleuchte ELN PRO bietet 10% mehr Licht bei gleicher Leistung im Vergleich zu unserer Standard Variante, stufenlose Dimmbarkeit und einen flexiblen Spannungsbereich von 12-30V – ideal für Anwendungsgebiete in Arbeitsbereichen mit wenig Platz. Erfahren Sie mehr über die Konfigurationsmöglichkeiten der ELN-PRO.
Robust, drehbar, 7 Längenvarianten – unser Allrounder unter den LED Industrieleuchten. Optimiert für raue Industrieumgebungen. Beständig gegen Öl- sowie Kühl – und Schmierstoffe (Schutzart IP67). In der ESG Variante ist sie zusätzlich gegen Beschuss von Metallspäne und Funkenschlag resistent.
Erfahren Sie mehr über die Eigenschaften der LED LR40.
Unsere LED Industrieleuchten werden durch Steckverbinder M8, M12 versorgt.
Erfahren Sie mehr über unser LED Zubehör.
Stufenlose Dimmbarkeit
Flexibler Spannungsbereich von 12-30V
Die LED Aufbauleuchte LR40 PRO bietet 10% mehr Licht bei gleicher Leistung im Vergleich zu unserer Standard Variante, stufenlose Dimmbarkeit und einen flexiblen Spannungsbereich von 12-30V – ideal für Anwendungsgebiete mit rauen Industrieumgebungen. Beständig gegen Öl- sowie Kühl – und Schmierstoffe und gegen Beschuss von Metallspäne und Funkenschlag (Schutzart IP67).
Erfahren Sie mehr über die Eigenschaften der LED LR40-PRO.
Die LED Arbeitsplatzleuchte mit integrierter Dimmfunktion durch einen Taster direkt an der Leuchte ist besonders effizient und homogen. Dank der Diamond Prism Abdeckung sorgt sie am Arbeitsplatz für eine gleichmäßige und blendfreie Ausleuchtung der Arbeitsfläche. Es sind drei verschiedene Montagesets erhältlich, um sich den Gegebenheiten ihres Arbeitsplatzes anzupassen. Die Möglichkeit zum durchschleifen mehrerer APLN Leuchten erleichtert die Installation. Mit 230 V~ kann die Leuchte zudem bequem an Handarbeitsplätzen angeschlossen werden und ist standardmäßig in drei verschiedenen Längen erhältlich.
Erfahren Sie mehr über die Eigenschaften der LED APLN.
In unserem Glossar lesen Sie alle Details zur LED-Technologie unserer Industrieleuchten.
Starten Sie ihre Karriere im #teamSangel.
Starten deine Zukunft mit #teamSangel.
Wir bieten eine Vielzahl vorgefertigter Leitungen, realisieren aber auch Ihre individuellen Kabelkonfektionen zu attraktiven Konditionen.
Ihre Antriebssysteme, unsere Leitungen: Wir verbinden Servoumrichter und Motor für alle Herstellerstandards.
Ihre Konstruktion lässt keine Standardleitung zu? Wir erstellen maßgeschneiderte Leitungskonfektionen für Ihren individuellen Fall.
In einem persönlichen Gespräch erörtern wir gerne mit Ihnen, wie sich eine Partnerschaft mit uns gestalten lässt und welchen Nutzen wir für Sie stiften.
In diesem Glossar rund um Kabelkonfektionen erfahren Sie alle Details zur LWL- und BUS-Technologie in der industriellen Kommunikation u.v.m.
Mit uns als Partner für Systembaugruppen sparen Sie Beschaffungskosten, Beschaffungsaufwand und Ihre kostbare Zeit.
Holen Sie sich die neuesten Broschüren von SANGEL® zu den Themen Kabelkonfektionen und LED Industrieleuchten – jetzt herunterladen!
Schnell, einfach, spezifisch – finden Sie die Maschinenleuchte, die zu ihren Bedürfnissen passt.
Nehmen Sie gerne Kontakt mit uns auf. Wir freuen uns auf Sie.
Nehmen Sie gerne Kontakt mit uns auf. Wir freuen uns auf Sie.
Wir sind ihr Experte im Bereich der LED Industrieleuchten, Kabelkonfektionen und Systembaugruppen. Lernen Sie uns, unsere Werte und Visionen näher kennen.
Sie möchten einen Regelverstoß im Unternehmen melden? Hier nehmen wir Ihre Hinweise entgegen – auf Wunsch vollkommen anonym.
Sangel Systemtechnik GmbH
Bechterdisser Str. 67
33719 Bielefeld